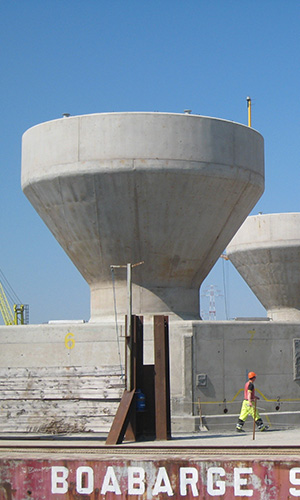
During the last 100 years concrete has become the most common material for man-made structures. Steel-reinforced concrete is cheap, needs no maintenance, has a high structural strength and is mouldable and fire resistant.
Under normal circumstances, the steel reinforcement (rebar) is encased in an alkaline environment and would not suffer from corrosion. However, concrete is sometimes used in an environment where chlorides may enter the concrete and attack the rebar. Such a circumstances are car parkings, tunnels where de-icing salts may attach concrete floors and support poles. Or concrete quay walls and jetties in harbours but also bridges, concrete bassins, foundation piles etc.
Concrete rebar corrosion comes in different stages : first a change in appearance (discoloration, blemishes) occur. Later on cracks are noticed at the surface. The third stage is the disruption with major spalling of concrete.
Concrete inspections are executed by visual inspections and a hammer survey to detect hollow areas. Another interesting method are electrical potential surveys, so called mapping, which may be executed to determine the areas with the highest corrosion attacks.
One of the best long term solutions for corrosion prevention of rebar is the use of cathodic protection.
Ask Anotec’s engineering department to engineer your concrete corrosion issues. We are eager to make you a competitive offer which comply with your needs for a long term corrosion protection.